Remote production demonstrated live at SportsInnovation 2024
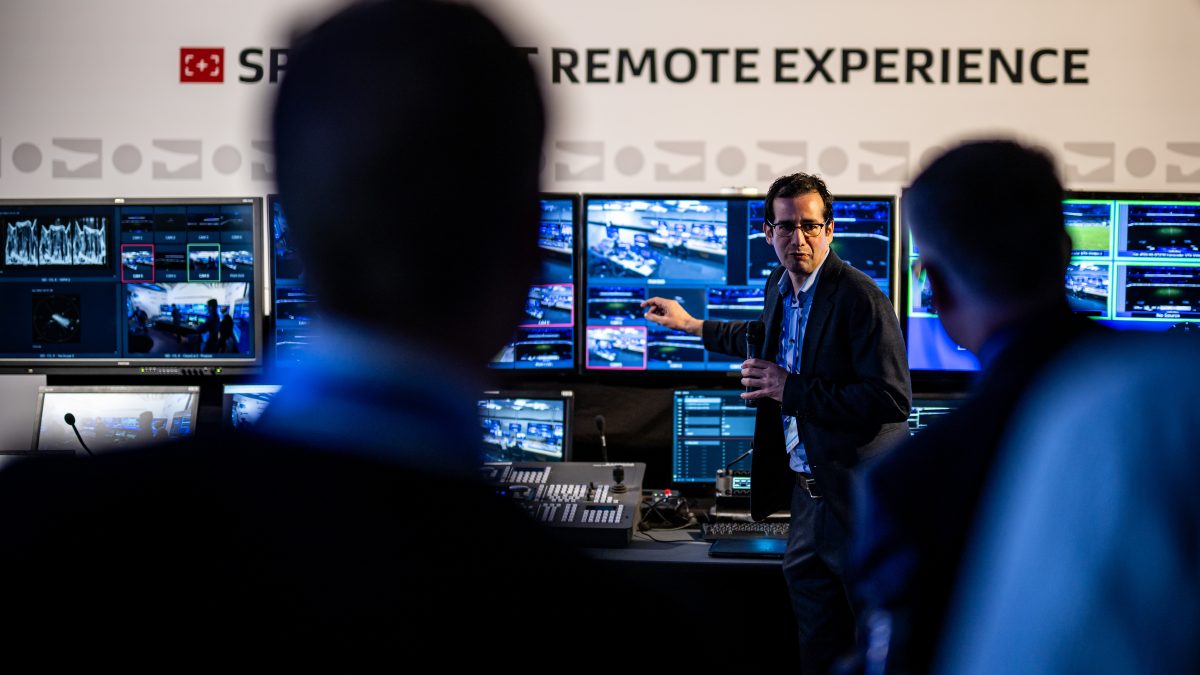
15 May 2024 – Simpler, more efficient, more sustainable: Highlights at SportsInnovation 2024 included the presentation and real-life demonstration of a pioneering IP-based remote production concept. By employing innovative technologies and a centralised production studio, this approach can reduce the technical complexity and effort involved in the production of sport events substantially while benefiting from significant synergies.
During four Innovation Games at this year’s SportsInnovation, the DFL, its partners and exhibitors demonstrated the latest technologies live on pitch. These matches were produced in two parallel processes, conventionally and remotely. The live remote production was demonstrated jointly by DFL subsidiary Sportcast and several of its partners.
Streamlined transmission minimises resource utilisation
The cameras at Düsseldorf’s MERKUR SPIEL-ARENA were the same as those used for typical Sportcast productions. Since the camera heads support the JpegXS compression format and are streaming-ready, they were able to transmit their signals directly, without a base station, to the Cologne-based remote production studio via a small hub located at the stadium. Video and sound post-synchronisation, which is required in other set-ups, was unnecessary. By employing an IP-based ST2110 production network using existing data transmission cabling inside the stadium, all signals were available in fully synchronised form throughout the network. Signal compression and decompression occurred in near-real-time, resulting in a very low latency of just a few milliseconds.
The equipment used at the stadium was the same as in a traditional production scenario. However, no broadcast vehicle was needed at the “TV compound”, the space normally reserved for this purpose – all signal processing equipment was housed in a small case that could easily be accommodated in the cable room. This simplified arrangement did not compromise system performance in any way, which was the same as always.
The entire production team operated from the remote studio in Cologne, which included the director’s video control station, two workstations for the slow-motion (slomo) operators, the video engineering room and staff, as well as the sound and production engineering stations. The hybrid production approach involved software-based processes such as video mixing and multi-viewer processing.
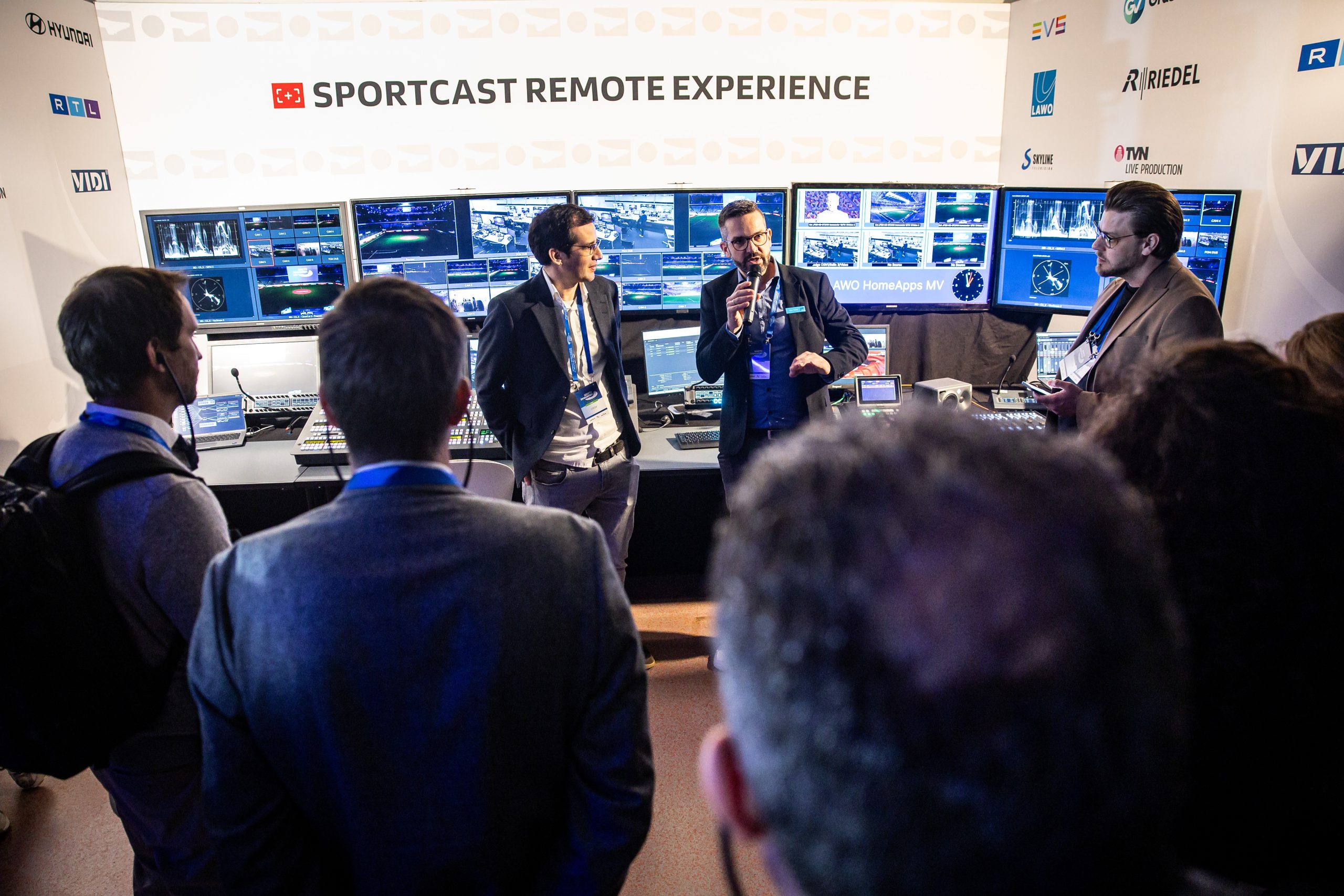
Centralised production creates synergies
This streamlined technical set-up, when combined with centralised production, creates far-reaching synergies for the production environment of the future: at a fully-equipped production centre that provides comprehensive technical resources, any type of programme can be produced with substantially reduced effort.
The operating procedures for the technicians in this remote production test case were the same as in a conventional scenario; they were able to work on familiar equipment without having to change their routines or requiring training.
Low energy consumption a key benefit
What was entirely new was the electricity source that had been chosen: The entire energy came from two e-vehicles. One electric passenger car fitted with a household-type outlet is enough to power this kind of production equipment. The second e-vehicle was provided as an emergency back-up only. If renewable energy, such as photovoltaic panels, is used to charge the car batteries in such a scenario, an entirely carbon-neutral production environment can be created.
InnoLab showroom attracts the crowds
The unique selling point of the event – innovations you can experience and touch – was also fully realised in the exhibition area: for the first time, visitors were able to test the latest technologies and ideas from exhibiting companies live in the “Innovation Lab”. As a major point of attraction, the DFL showroom featured a fully-equipped production studio including all required director’s, slomo, video and sound engineering workspaces where visitors were allowed to have a go at operating the production equipment themselves. While this had no effect on the real-life production of the innovation matches, the showroom studio featured the same equipment as the remote studio in Cologne, using the same camera and microphone live signals. This provided media partners and other interested visitors with an opportunity to familiarise themselves hands-on with the production environment of the future, try out the look and feel, and see for themselves that state-of-the-art technology can easily be deployed to set-up an additional, unilateral production centre at any location.